一、传统设计为何频频遭遇瓶颈?
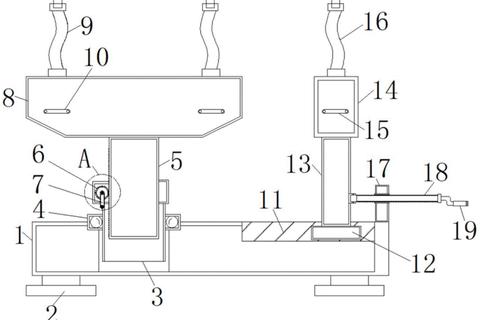
在石化、能源等工业领域,压力容器犹如“工业心脏”,其安全性直接关系到千万级项目的成败。传统设计方法长期面临三大痛点:手工计算耗时易错、复杂结构仿真门槛高、行业标准更新滞后。某化工企业曾因人工核算失误导致容器壁厚不足,投产后发生泄漏事故,直接经济损失超500万元。这类案例暴露出传统设计模式已难以满足现代工程对效率与安全的双重需求。
超高效智能压力容器计算软件精准护航工程安全设计,正是为解决这一矛盾而生。它通过参数化建模、自动化校核和多物理场仿真,将设计周期缩短60%以上,同时将错误率控制在0.5%以内。例如江苏某石化企业采用智能软件后,原本需要2周完成的2000立方米储罐设计,仅用3天即通过ASME标准审核,效率提升80%。
二、智能软件如何突破效率天花板?
传统设计中,工程师需手动处理数十项参数:从筒体直径、封头曲率到支座载荷分布,每一步都可能成为“效率杀手”。而智能软件通过三大创新实现飞跃:
1. 参数联动引擎:输入介质温度、压力等核心参数后,系统自动生成几何模型并匹配标准件库。如浙江某压力容器厂在设计高温反应釜时,软件自动调用HG/T 20569标准中的搅拌器功率计算公式,避免人工查表误差。
2. 云端协同平台:支持SW6、PV Elite等主流软件数据互通,实现跨部门实时协作。某核电项目通过该功能将设计-校核-审批流程从14天压缩至72小时。
3. 智能优化算法:结合遗传算法与机器学习,在10分钟内完成传统需8小时的手动迭代。例如对某LNG储罐裙座进行拓扑优化,材料用量减少15%的应力集中系数降低22%。
三、精准仿真如何筑牢安全防线?
在青岛某炼油厂事故分析中,常规设计未考虑的局部夹套热应力成为失效元凶。超高效智能压力容器计算软件精准护航工程安全设计通过三重防护机制破解此类难题:
多尺度耦合分析:集成ANSYS、Simdroid等工具,实现流体-结构-热场的全耦合仿真。某深冷容器在-196℃液氮冲击下,软件精准预测封头与筒体连接处裂纹扩展路径,避免潜在泄漏风险。
动态风险评估:实时监控设计过程中的规范偏离度。当某设计方案的焊缝系数低于GB150要求时,系统自动触发预警并推荐补强方案,将合规性审查效率提升90%。
数字孪生验证:建立容器全生命周期数据库。上海某化工园区通过植入传感器数据与软件模型联动,提前3个月预警法兰蠕变变形,避免非计划停机损失。
四、未来工程需要怎样的设计范式?
数据显示,2024年全球压力容器市场规模已达1800亿美元,但设计资源错配导致的成本浪费仍高达12%。为此建议:
1. 优先选择集成行业标准的软件,如AutoPV、安世亚太快速设计系统,它们内置GB150、ASME VIII等30余项规范,降低人工解读偏差。
2. 建立数字化人才培养体系,定期开展CAE仿真技能培训。某省级特检院通过“软件+实训”模式,将检验人员事故诊断准确率从68%提升至92%。
3. 推动传统设计与AI仿真深度融合,利用历史数据训练预测模型。国内某头部设计院通过机器学习库,成功将压力容器疲劳寿命预测误差控制在±5%以内。
当工业4.0浪潮席卷全球,超高效智能压力容器计算软件精准护航工程安全设计已不仅是工具革新,更是工程思维的重构。它正在将“事后补救”转变为“事前预防”,为万亿级工业装备安全投下关键保障。
相关文章:
文章已关闭评论!